Watch: Engineers Build a Drivable Full-Size Bugatti with LEGO Technic
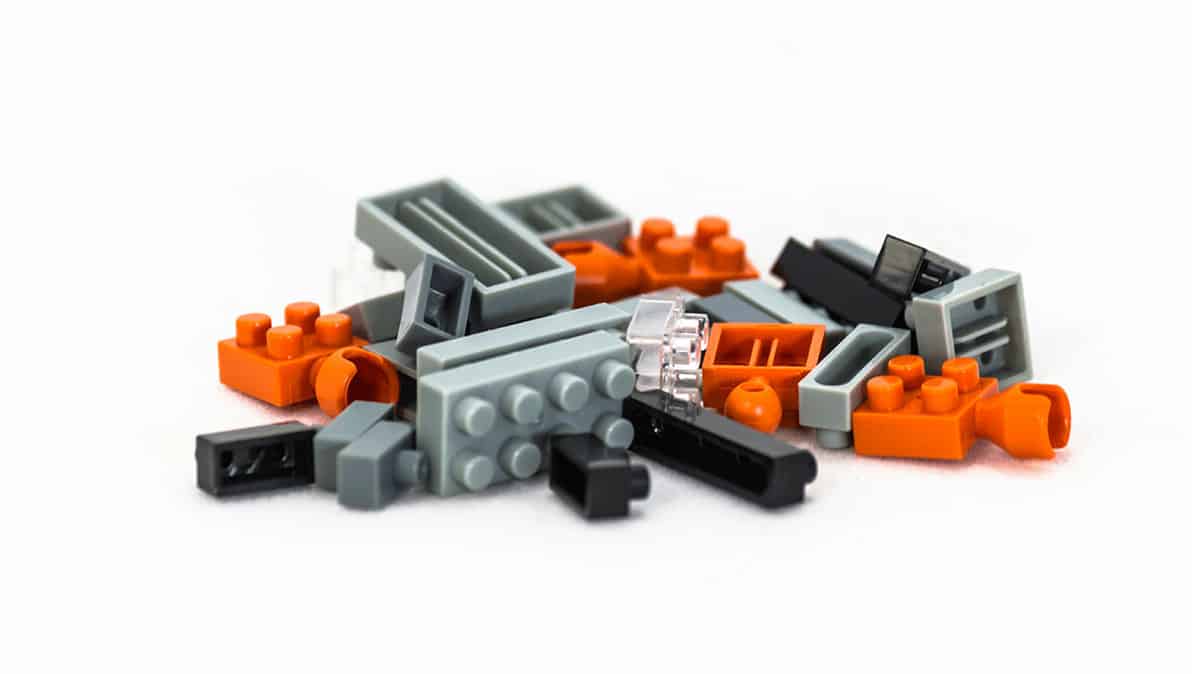
With LEGO Technic, you can Build Anything for Real
You can build anything out of LEGO, seriously anything. LEGO engineers designed and constructed a drivable full-size Bugatti Chiron out of LEGO Technics. Let’s take a closer look at this fun engineering feat.
How did the LEGO Technic Bugatti Chiron Project Get Started?
The LEGO Technic team wanted a challenge their own motto “With LEGO Technic, You can Really, Build for Real.” They decided to push the limits by creating a drivable Bugatti Chiron from 90% LEGO Technics that a human could drive.
Was the idea even possible?
The LEGO team was determined to find out.
The Car
The LEGO Bugatti Chiron has over 1 million LEGO pieces, including all of the motors, gears, pneumatics, and even the door hinges. Engineers didn’t use any glue to hold the LEGO pieces together.
Because the car has no straight lines along the surface, the engineers created small triangles connected with flexible pieces to “skin” the outside of the car. The results are smooth and impressive!
The car gets its power from a matrix of 2304 stacked power function LEGO motors. The LEGO gears were a concern because they had to move a 1.5-ton vehicle. The engineers tested gears made from metal, Kevlar, and carbon fiber for the vehicle. In the end, the LEGO gears worked BETTER than the gears from the other materials.
The wing on the rear of the Bugatti pushes the design over the edge. It uses LEGO power functions and pneumatics to raise out of the car and adjust, just like the real car.
LEGO engineers spent more than 13,000-man-hours working on the car. Every element was assembly by hand! It had to be sturdy enough to survive transportation and be able to drive.
The Test Drive
Andy Wallace, the official test drive of the real Bugatti Chiron, waited at Germany’s Ehra-Lessien test track to see if the LEGO Bugatti would stand the ultimate test. After the car arrived, there was a malfunction in a non-LEGO chain.
Would all the work and man-hours invested in the project be for nothing?
Luckily, the team on the ground figured out the problem and got the car on the road. Andy got in the car and put the LEGO gas petal to the preverbal metal.
The car took off down the track. IT ACTUALLY WORKED!
It’s incredible what standard parts and ingenuity can accomplish!
Watch the full story:
Mechanical Engineers Benefit from Reuse like LEGO
Here at PARTsolutions, we believe that engineers should focus on innovation instead of recreating supplier parts that are readily available. There is an engineering philosophy called, “Think in Standard Parts.” The idea is to select as many “standard” parts as you can upfront, and custom design only the parts you need.
LEGO is the perfect illustration of how to think in standard parts. People use LEGO to create mind-blowing structures, robots, and yes, even cars. I couldn’t help but share this amazing story about how LEGO engineers designed and built a fully working car. It lines up perfectly with how engineers can use standard parts from suppliers like fasteners, clamps, extrusions, bearings, and motors and custom design only a few parts from scratch.
Learn More: Get These Free eBooks
The Basics of SPM
SPM vs. Classification
MBE / MBD for Mfgs
Joseph Lewin
Latest posts by Joseph Lewin (see all)
- What Industrial Marketers Need To Know About STEP files - March 22, 2022
- How to Differentiate Components in a Commodity Market - February 23, 2022
- Field Research is Vital for Industrial Marketers - February 18, 2022